How Does an Electric Car Work?
Electric cars store energy in rechargeable batteries and use one or more electric motors to power the vehicle – no gas required! What sets an electric car, or BEVs (battery electric vehicles) apart from other vehicles is that they run purely on electricity.
Electric cars are a lot less complex than gasoline cars. They have significantly fewer moving parts. They are:
- No oil changes
- No transmission rebuilds
- Less wear and tear on the braking system
Lower maintenance costs are just one of the biggest advantages of going electric. To understand these advantages fully, you'll want to first answer the critical question: How do EVs work?
How Electric Car Batteries Work
If you’re used to gasoline vehicles, for the sake of simplicity, think of electricity as fuel; the rechargeable battery as the fuel tank; and the electric motor as the engine.
The battery is the largest, most expensive, and most important component of an electric car. It stores the electrical energy needed by the car and powers its components. Most modern electric vehicle batteries are lithium-ion or lithium-iron-phosphate, as they store high levels of energy while remaining relatively lightweight. Typically, a bigger battery (measured in kilowatt-hours, or kWh) means more electric range.
The battery pack is charged using an external power source – a charging plug is inserted into the car’s charge port. Think of the charging plug as the EV equivalent to a fuel nozzle at a gas station. The car’s on-board charger converts the plug’s electrical current to a format that can charge the battery, whether it’s AC (alternating current) – like the kind of power in our home wall outlets – or DC (direct current) – like the kind available at public fast charging stations.
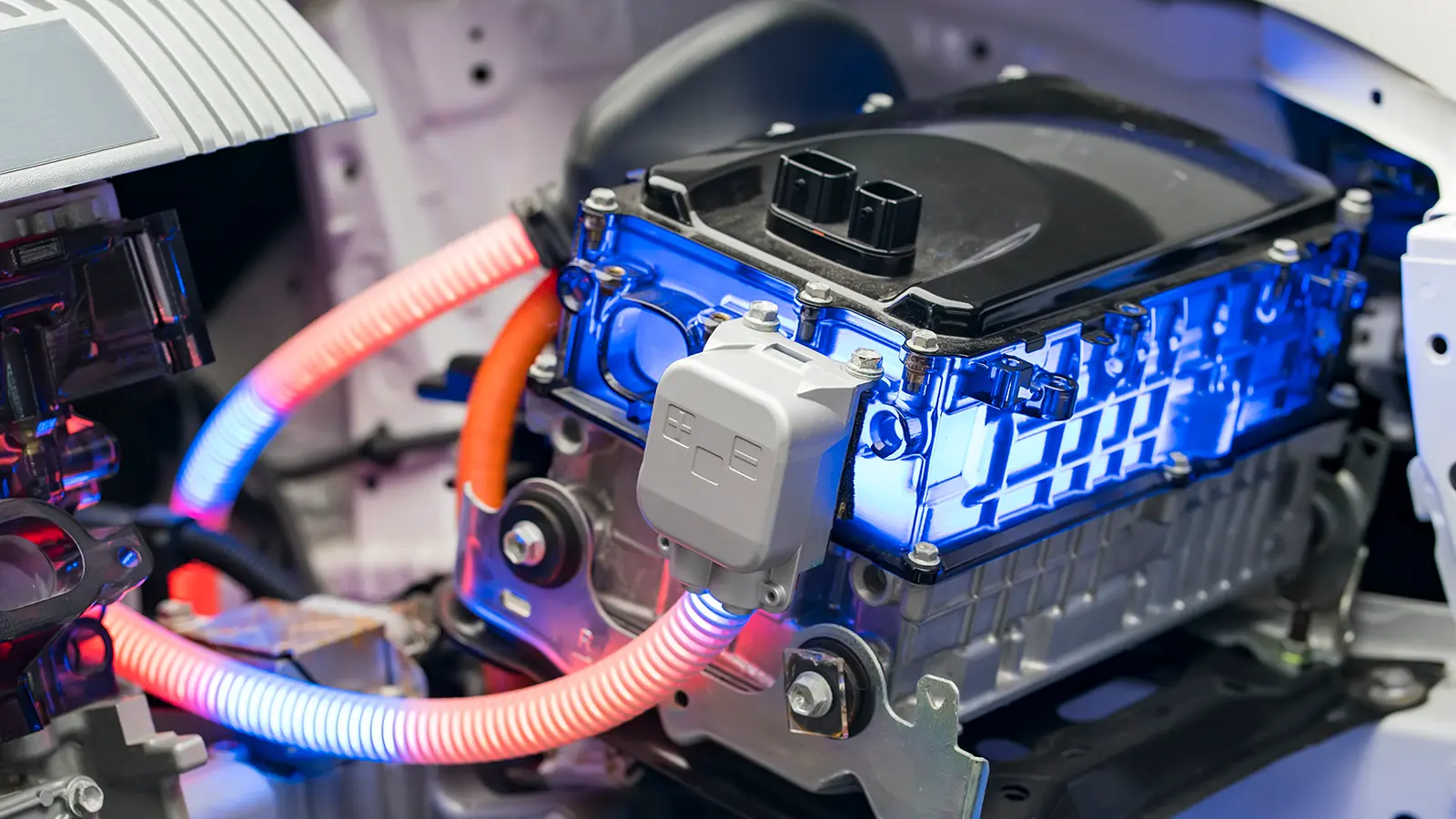
You Can Charge an Electric Car at Home
The battery pack is charged using an external power source – a charging plug is inserted into the car’s charge port. Think of the charging plug as the EV equivalent to a fuel nozzle at a gas station. You won’t need to look too hard to find the right power source. In addition to the many public EV charging stations available, you can even charge your EV at home!
Many new electric vehicles can charge up to 80% in about 30 minutes with a Level 3 fast charger (at a public station). If using a Level 2 charger at home, it could take up to 12 hours for a full charge. Just let it juice up overnight while you sleep!
Electric Vehicle Technology: A Deeper Dive
Power electronics are another important component in electric cars. They manage the flow of electrical energy delivered by the traction battery to the electric motor. The power electronics also manage the speed at which the motor turns and control the torque the motor produces.
The power electronics also help distribute electrical energy from the traction battery to the auxiliary vehicle systems, such as the lighting, heating, ventilation, and infotainment systems.
Rather than the main battery, a separate auxiliary battery – identical to the ones found in gasoline vehicles – is responsible for powering these systems. This battery is charged by the DC/DC converter, which converts high-voltage DC power from the traction battery into the low-voltage DC power required to power the auxiliary systems.
The vehicle thermal management system also should be mentioned. It helps ensure that the vehicle’s batteries are operating within the correct temperature range. This ensures the car isn’t likely to overheat on you—another factor that cuts down on maintenance costs and leads to vehicle longevity.
What is Regenerative Braking?
One of the cool things about electric motors is the “regenerative braking” function. When you take your foot off the accelerator (not gas!) pedal, the motor acts in reverse and converts the car’s forward motion back into electrical energy. The energy is then sent back to the battery –recovering energy that would otherwise be wasted. It won’t come close to fully charging your electric car’s battery, but regenerative braking does help give you a little bit of extra range.

How Electric Car Motors Work
Using electrical energy from the battery pack, the EV motor converts that energy into mechanical energy, which drives the wheels. Most electric vehicles don’t have a transmission with multiple speeds, so there are no gears to shift. Depending on the number and placement of the motors, an electric car can either be front-wheel drive (FWD), rear-wheel drive (RWD), or all-wheel drive (AWD). Some electric cars even have a motor at each wheel!
Most EV motors have two main components: the stator, which is the stationary part of the motor, and the rotor, which is the moving part of the motor. While each piece has its own complex design, they serve a single simple purpose: to enhance efficiency for drivers. Electric car motors convert about 45% more electrical energy into mechanical energy than gas engines!