Green Car Technology
Green vehicles may look like ordinary cars, but under the hood and beneath the floor, they’re powered by some of the most advanced technologies in the automotive world. Whether you’re just starting your research or are ready to dive deeper, this article introduces the core systems that make green cars cleaner, smarter, and more efficient than traditional gas vehicles.
What Makes a Car “Green”?
A green car uses less gasoline, or none at all. Its powertrain is designed to reduce or eliminate tailpipe emissions, and it often includes energy-efficient systems that make better use of power, from regenerative braking to advanced aerodynamics. Green vehicles include:
- Hybrid cars (HEVs) that combine a gas engine with an electric motor
- Plug-in hybrids (PHEVs) that add a larger rechargeable battery and electric-only range
- Battery electric vehicles (BEVs) that run solely on electricity
- Fuel-cell electric vehicles (FCEVs) powered by hydrogen
Each of these vehicle types uses specialized green technology. Let’s explore the major systems that set them apart.
Electric Motors: Quiet, Instant Power
Unlike internal combustion engines, electric motors don’t burn fuel. Instead, they convert electricity into motion through electromagnetic fields. The benefits are immediate:
- Instant torque for quick acceleration
- Smooth, quiet operation
- No exhaust or tailpipe emissions
In many EVs, the motor is mounted between the wheels, either up front, in the rear, or both for all-wheel drive.
Batteries: The Heart of the EV
Electric cars are powered by large battery packs made of lithium-ion cells, similar to those in smartphones, just much bigger and more robust. These batteries store energy and feed it to the motor when you press the accelerator. Key features include:
- Capacity measured in kilowatt-hours (kWh), which affects range
- Built-in thermal management systems to maintain battery health
- Charging ports that allow recharging from wall outlets or public stations
The most efficient batteries use rare earth elements like lithium, nickel, and cobalt, though newer chemistries are now emerging to reduce costs and environmental impact.
Regenerative Braking: Recycling Energy
Green cars don’t just use energy efficiently; they also recover energy while driving. Regenerative braking captures some of the energy that’s normally lost as heat when you slow down, then stores it back in the battery. This process:
- Helps extend driving range
- Reduces wear on brake components
- Makes stop-and-go driving more efficient
Onboard Electronics and Smart Software
Today’s green vehicles are packed with digital systems that monitor, optimize, and enhance performance:
- Battery management systems (BMS) that track charge levels, temperature, and health
- Energy efficiency displays to help you drive smarter
- App connectivity for tracking charging sessions, planning routes, or pre-conditioning the cabin
Some EVs also receive over-the-air software updates, just like your phone, to add features or improve driving performance over time.
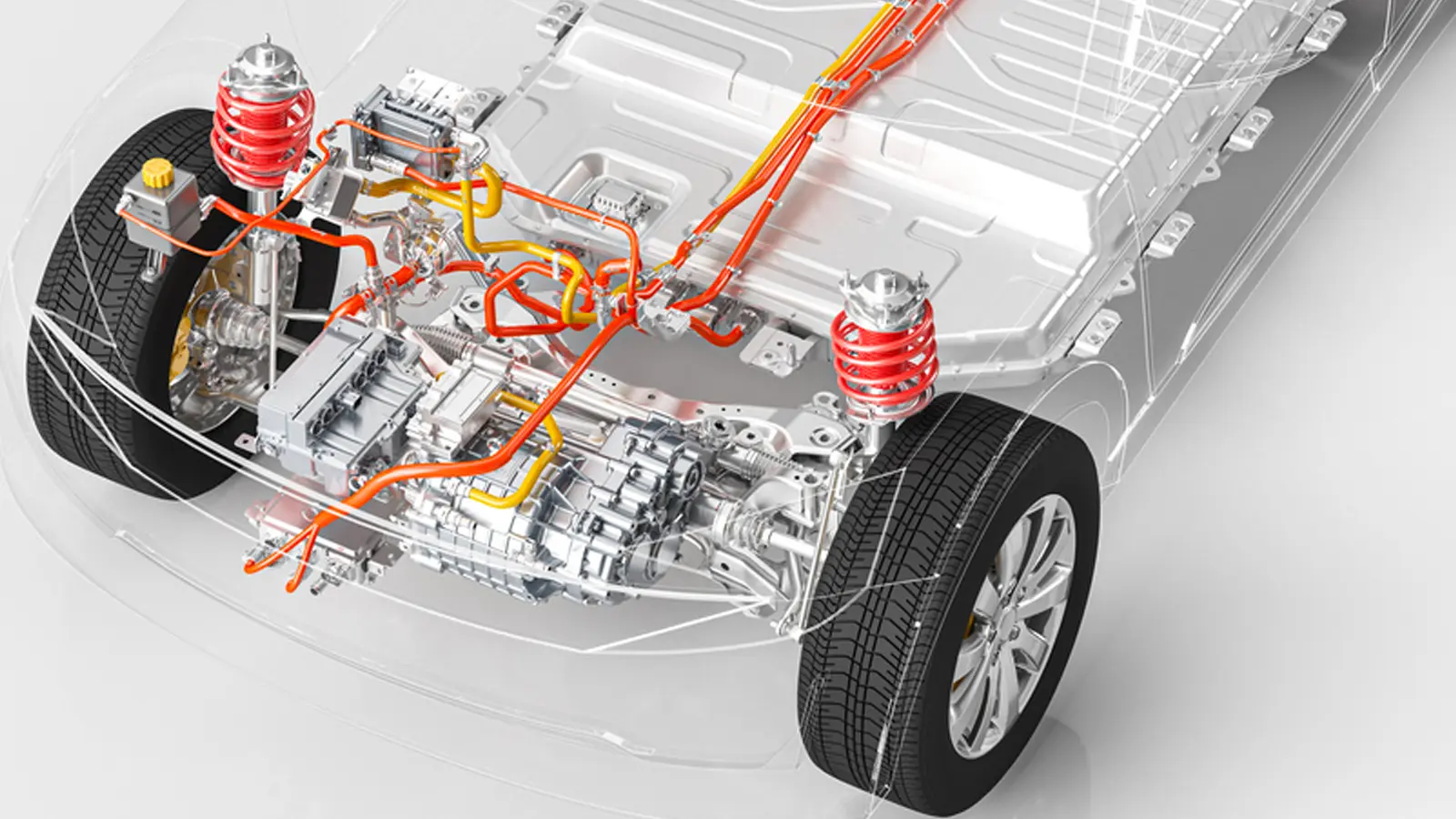
Charging Systems and Infrastructure
Battery electric vehicles (and plug-in hybrids) use onboard chargers to convert AC or DC electricity into stored energy. Owners can charge:
- At home with Level 1 (standard outlet) or Level 2 (240V) charging
- On the go with public stations, including DC fast charging for long trips
Charging connectors vary by vehicle and location, but many new models are adopting a universal standard, helping make EV ownership more convenient across North America.
Aerodynamics and Lightweight Materials
Green cars are often designed with advanced materials and sleek shapes to maximize efficiency. This includes:
- Low drag coefficients for better highway range
- Lightweight frames and body panels to offset heavy batteries
- Recycled and sustainable interior materials, such as plant-based fabrics or vegan leather
These improvements not only reduce environmental impact but often improve performance and comfort as well.
Fuel Cells and Hydrogen Power
Some green vehicles use hydrogen fuel cells instead of batteries. In these cars, compressed hydrogen gas is converted into electricity using an electrochemical process, emitting only water vapor as a byproduct.
- Refueling takes just minutes
- Driving range can exceed 300 miles
- Currently available mostly in California and a few pilot markets
While still limited in availability, hydrogen technology may play a larger role in future clean transportation, especially for heavy-duty vehicles and long-distance fleets.
The Bottom Line
Green cars use some of the most exciting innovations in the auto industry today, from electric drivetrains and regenerative braking to smart software and new fuels. These technologies not only make vehicles cleaner but also more fun to drive, easier to maintain, and more affordable to own over time.
Whether you're looking at hybrids, plug-in hybrids, or fully electric cars, understanding these systems will help you make smart decisions and feel more confident about your path toward cleaner driving.
Ready to Keep Learning?
Continue building your knowledge of green car essentials:
← Go Back: What Are Green Cars?
Discover Next: Green Car Acronyms and Terms Explained →